Sambalpuri Saree
Sambalpuri sarees are a traditional handwoven textile hailing from the western region of Odisha, India. They are renowned for their craftsmanship, unique designs, and vibrant colors. Sambalpur, Bargarh, Sonepur, and Boudh districts in Odisha are the main centers where these sarees are woven. Sambalpuri sarees are popular among Odia women for special occasions, festivals, and cultural events. They are also cherished as valuable heirlooms passed down through generations.
Key features of Sambalpuri saree
Ikat Technique: Sambalpurisarees are primarily known for their use of the “Ikat” technique, where the yarn is tie-dyed before weaving to create intricate patterns and designs. This technique involves precise tying and dyeing of yarns to achieve the desired patterns on the final fabric.
Natural Dyes: Traditionally, natural dyes were used to color the yarn, giving the sarees a rich and organic appearance. The dyes were derived from materials like indigo, madder root, and various leaves, giving the sarees a distinctive and earthy appearance. With time, the use of synthetic dyes became more prevalent due to their cost-effectiveness and ease of availability.
Motifs and Designs: Sambalpurisarees feature a wide range of motifs inspired by nature, mythology, and cultural symbols. Some common designs include fish, conch shells, flowers, elephants, and geometrical shapes. Each motif holds its own symbolic significance.
Varieties: Sambalpuri sarees come in various styles, including Sonepuri, Bomkai, Pasapali, and Barpali, each with its distinct design elements and weaving patterns.
Handwoven Artistry: These sarees are intricately handwoven by skilled weavers who have inherited the art of Sambalpuri weaving from their ancestors.
also read about Indian Sarees and types
History of Sambalpuri Saree
The art of weaving Sambalpuri sarees has been passed down through generations, and the craft holds a significant place in the socio-economic fabric of the region. The exact origin of Sambalpuri sarees is not precisely documented, but it is believed to have flourished around the Sambalpur and Bargarh districts of western Odisha. The weaving tradition in the region is said to date back several centuries, with evidence suggesting that the art form existed during the medieval period.
The influence of the Ikat technique used in Sambalpuri sarees can be traced back to Southeast Asian countries, where similar techniques were employed in their textiles. Over time, these weaving techniques traveled along trade routes and found their way to the Indian subcontinent. Sambalpuri sarees gained prominence and popularity during the rule of the Bhanja dynasty, which ruled the region during the 12th to 19th centuries. The Bhanjas were patrons of art and culture, and their support played a vital role in the growth of the weaving industry in the region.
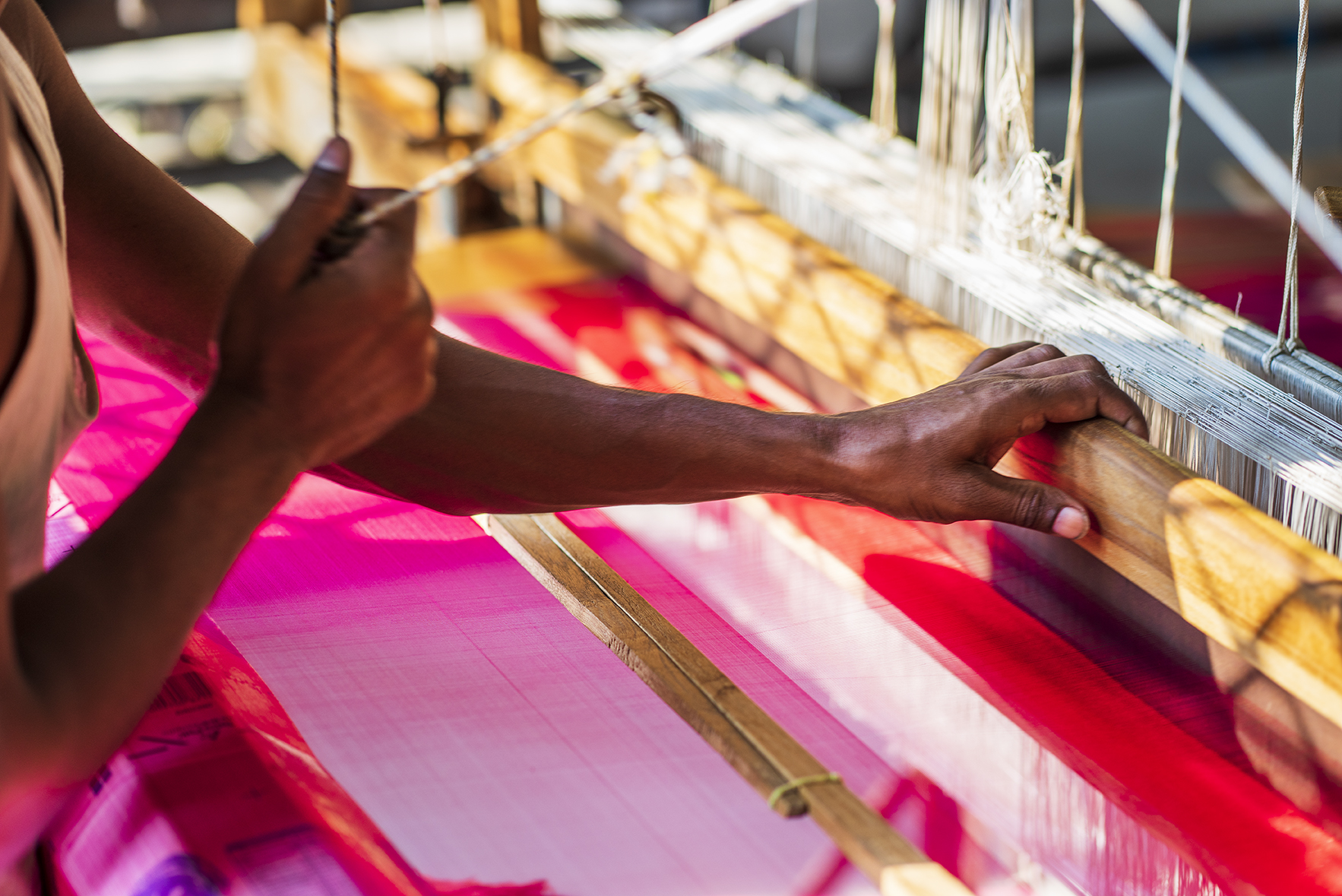
Manufacturing of Sambalpuri sarees
The entire process of making these sarees involves several steps, each requiring skill and precision. Here’s below step-by-step information on how Sambalpurisarees are made:
- Designing and Drafting: The process begins with the design stage, where skilled artisans create intricate patterns and motifs on graph paper or other templates. These designs are then converted into weaving instructions, known as “nabakatha” or “tanabana,” which serve as a guide for the weavers during the weaving process.
- Yarn Selection: High-quality yarn is selected for the sarees. Traditionally, cotton and silk yarn were used, but nowadays, a blend of both natural and synthetic yarns is common to cater to different preferences and market demands.
- Dyeing: The next step is dyeing the yarn to achieve the desired colors for the saree. If natural dyes are used, they are prepared by extracting colors from plants, roots, or minerals. However, synthetic dyes are increasingly used due to their convenience and availability.
- Tie-Dyeing (Ikat Technique): This is the defining step in making Sambalpuri sarees. The yarn is tied at specific intervals using rubber bands or threads to resist the penetration of the dye. The tying process creates intricate patterns and motifs that are characteristic of Sambalpurisarees.
- Drying: After tie-dyeing, the yarn is left to dry under the sun, allowing the colors to set and the patterns to take shape.
- Setting the Warp: The dyed and dried yarn is then arranged on the loom to set the warp (lengthwise yarns). The weaver follows the “nabakatha” to ensure that the patterns align correctly.
- Weaving: The actual weaving process begins, and the weaver interlaces the dyed warp yarns with the weft yarns (horizontal yarns) to create the fabric. The patterns emerge as the dyed yarns are woven into place.
- Finishing: Once the weaving is complete, the saree undergoes a finishing process, which includes cutting the extra threads, trimming the edges, and checking for any imperfections.
- Embellishments: Depending on the design, some Sambalpurisarees may have additional embellishments like zari work (gold or silver thread), beadwork, or embroidery, which further enhance their beauty.
- Washing and Starching: The finished saree is washed to remove any residual dye or impurities. After washing, the saree is starched and ironed to give it the desired texture and finish.
Despite the challenges of modernization, the weavers continue to preserve this ancient art form, ensuring its survival and global recognition. With their vibrant colors, unique designs, and cultural significance, Sambalpuri sarees remain